Spritzguss-Maschinen – 24 Stunden, 7 Tage die Woche in Betrieb
Neben den beiden Maschinen zur Produktion von Flaschen, betreibt die Fabrik zehn weitere Spritzguss-Maschinen für die Verarbeitung von Kunststoff. Sie sind 24 Stunden am Tag und 7 Tage die Woche in Betrieb. Als wir da waren fertigte eine die Rollen für einen Heimtrainer, auf denen später die Reifen des Bikes aufliegen. Eine andere Maschine stellt während dessen die blauen Rollen für einen Tacx-Galaxia her.
Sobald das Spritzgussverfahren abgeschlossen ist, entfernen Roboter die fertigen Teile aus den Formen. Danach wird die Gussform wieder geschlossen, mit flüssigem Plastik befüllt, heruntergekühlt und öffnet sich wieder bevor der Roboterarm zurückschwengt und das nächste Teil entnimmt. Der ganze Vorgang dauert nur wenige Sekunden.
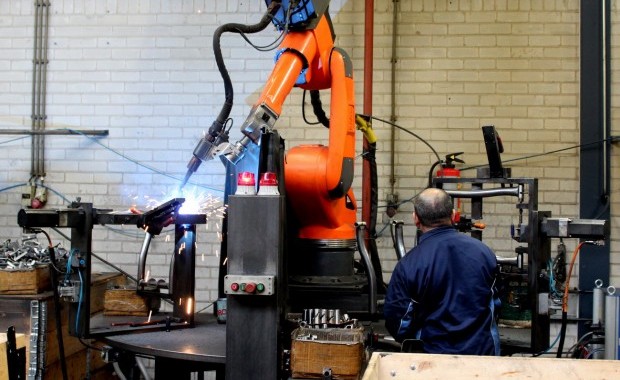
Das niederländische Unternehmen arbeitet seit 1979 mit Robotern und inzwischen sind in der ganzen Fabrik 20 davon im Einsatz. Die meisten Fertigungsverfahren sind mittlerweile voll automatisiert. Nur die Inbetriebnahme von neuen Gussformen für spezielle Teile und die dazu nötige Programmierung der Maschine, bilden eine Ausnahme.
Jede Maschine kann, je nach größe der Teile, der Höhe des benötigten Drucks und der Maschinengröße, eine bestimmte Menge produzieren. Kleinere Maschinen werden für die Herstellung kleinerer Teile und Größere für die Fertigung größerer Teile eingesetzt. Die blauen Rollen für den Galaxia gehören zu den größten Kunststoffteilen, die bei Tacx produziert werden und die dafür benötigte Maschine erzeugt den erforderlichen Druck, der zwischen 280 und 1,450 Tonnen liegt.
„Diese Art von Rollen sind einer der am schwersten zu produzierenden Teile die wir hier machen,“ erzählt Marcel de Bode. „Für gewöhnlich ist es sehr schwer, große aber dennoch dünne Kunststoffröhren zu bauen, die eine komplett glatte Oberfläche haben. Für die Entwicklung einer entsprechende Gussform brauchen wir mehr Zeit und die Rollen müssen deutlich länger gekühlt werden, bevor sie aus der Form entnommen werden können.“
Share